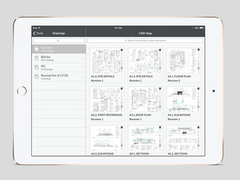
When creating a capacity planning strategy, you need to consider the expected growth of the workload, including any customer-driven growth and new features. You should then plan accordingly. Here are four common scenarios to consider: Lead, Lag, Match, Adjustment. Each scenario is unique and has its challenges as well as benefits. You should consider each of them carefully to ensure that your capacity planning is effective.
Lead strategy
Companies that have a plan for capacity planning are proactive about expanding capacity, expanding systems or resources before the demand increases. A lag strategy on the other side waits until demand rises before expanding capacity. The advantage of a lead strategy is that it avoids the risk of running out of capacity due to an unexpected increase in demand.
This strategy is effective in many situations but it is best when the volume of goods/services will be greater than expected. It can also help when demand rises quickly, such as during the holidays. Retailers can hire seasonal workers to help them staff their stores for more customers. It is also possible to increase headcount quickly with a lead strategy.
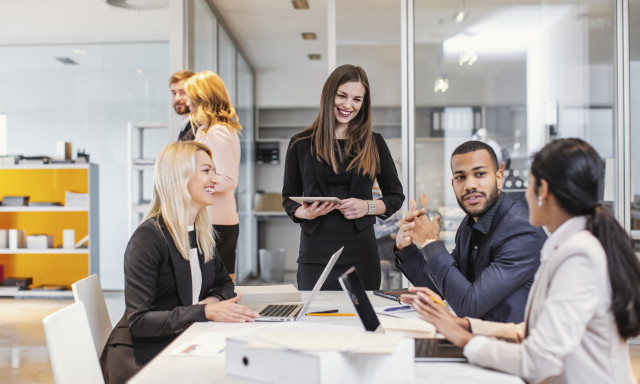
Lag strategy
To match demand and capacity, the Lag strategy is used for capacity planning. This strategy is less risky than the Lead strategy, but it requires a great deal more work and effort. It is also less risk-averse compared to the other strategies. The lead strategy, however, attempts to anticipate future demand and increases capacity accordingly. This strategy might not work for all organizations because of time constraints or resource limitations.
If you have a stable company model, the lag strategy may be a good choice. It prevents wasteful resources and excess inventory by only expanding production when demand for the product increases. This approach can cause stress in the process of training and hiring new employees. An aggressive lead strategy is, however, more aggressive. It anticipates future demands and meets them before their time.
Match strategy
The Match strategy can be described as the middle ground between Lead and Lag strategies in capacity planning. This strategy emphasizes incremental capacity increases, and not boosting demand ahead. This strategy is less risky for manufacturers than the others, and requires more planning. While it may not be cheap to increase capacity, it is much safer than the two other strategies.
Match strategies involve monitoring the current demand and analysing forecasts. This helps the company to quickly adapt to changes in demand. It is more work but it allows for quick and efficient pivots. It helps to streamline operations by making sure that the resources are available for future and current needs.
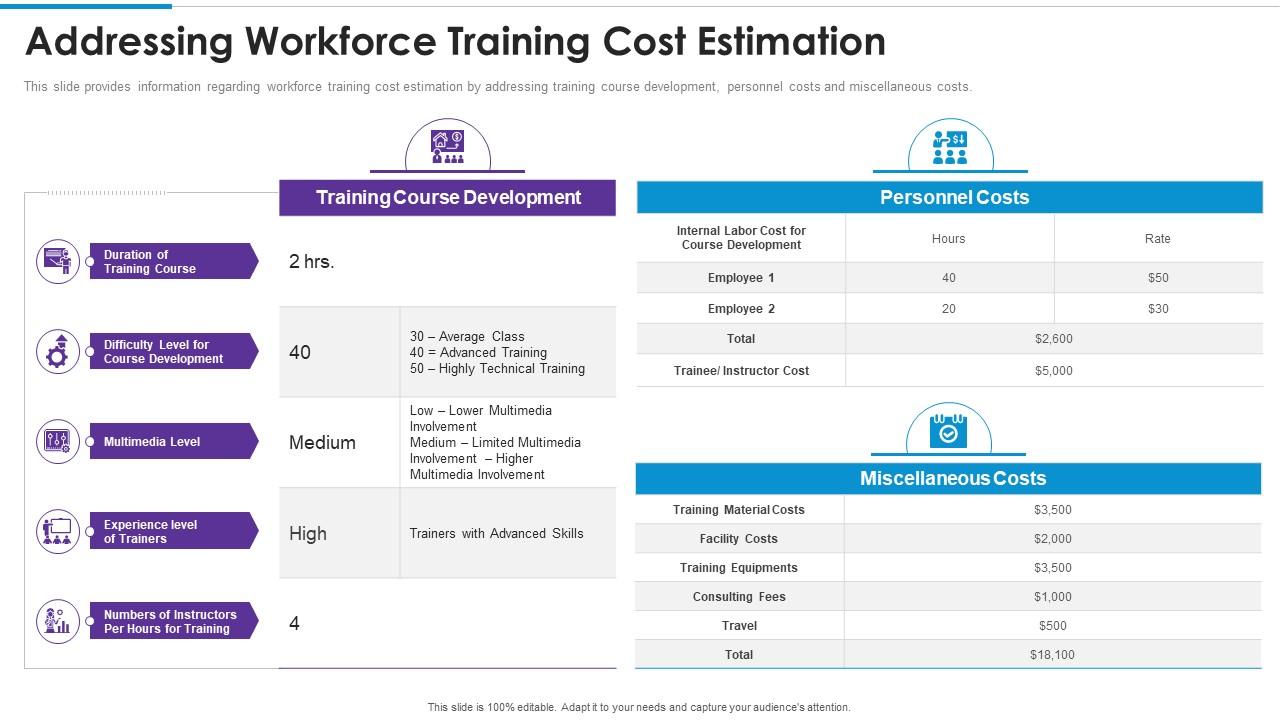
Adjustment strategy
A common strategy to manage supply chain capacity is the Adjustment strategy for capacity plan. This ensures that the supply network is always ready to respond to demand. It helps businesses to meet their deadlines and scale up their businesses. Choosing the correct strategy can increase the bottom line. The Adjustment strategy can help organizations meet their supply-chain needs more efficiently.
It forces organizations be more realistic in their estimation of their resources. Overestimating resources can cause low productivity and low employee morale. Over-allocating budgets can cause significant opportunity losses, since they could have gone towards continuous service improvement, innovation, pay, or employee compensation. Leaders must be realistic when forecasting their budgets.
FAQ
Six Sigma is so popular.
Six Sigma is easy to use and can lead to significant improvements. It can also be used to help companies identify and focus on the most important aspects of their business.
How do we build a culture that is successful in our company?
A company culture that values and respects its employees is a successful one.
It's based on three main principles:
-
Everybody has something of value to share
-
People are treated fairly
-
It is possible to have mutual respect between groups and individuals
These values are reflected in the way people behave. They will treat others with respect and kindness.
They will be respectful of the opinions of other people.
They encourage others to express their feelings and ideas.
Company culture also encourages open communication, collaboration, and cooperation.
People are free to speak out without fear of reprisal.
They understand that mistakes can be forgiven as long as they're dealt with honestly.
The company culture promotes honesty, integrity, and fairness.
Everyone knows that they must always tell truth.
Everyone knows that there are rules and regulations that apply to them.
People don't expect special treatment or favors.
What is the difference between TQM and Six Sigma?
The main difference between these two quality-management tools is that six-sigma concentrates on eliminating defects while total QM (TQM), focuses upon improving processes and reducing expenses.
Six Sigma stands for continuous improvement. It emphasizes the elimination and improvement of defects using statistical methods, such as control charts, P-charts and Pareto analysis.
This method has the goal to reduce variation of product output. This is accomplished by identifying the root cause of problems and fixing them.
Total quality management is the measurement and monitoring of all aspects within an organization. Training employees is also part of total quality management.
It is often used as a strategy to increase productivity.
Statistics
- As of 2020, personal bankers or tellers make an average of $32,620 per year, according to the BLS. (wgu.edu)
- Hire the top business lawyers and save up to 60% on legal fees (upcounsel.com)
- UpCounsel accepts only the top 5 percent of lawyers on its site. (upcounsel.com)
- 100% of the courses are offered online, and no campus visits are required — a big time-saver for you. (online.uc.edu)
- This field is expected to grow about 7% by 2028, a bit faster than the national average for job growth. (wgu.edu)
External Links
How To
How do I do the Kaizen Method?
Kaizen means continuous improvement. This Japanese term refers to the Japanese philosophy of continuous improvement that emphasizes incremental improvements and constant improvement. It's a process where people work together to improve their processes continuously.
Kaizen is one of Lean Manufacturing's most efficient methods. In this concept, employees who are responsible for the production line must identify problems that exist during the manufacturing process and try to solve them before they become big issues. This will increase the quality and decrease the cost of the products.
Kaizen is the idea that every worker should be aware of what is going on around them. Correct any errors immediately to avoid future problems. If someone spots a problem while at work, they should immediately report it to their manager.
Kaizen is based on a few principles. When working with kaizen, we always start with the end result and move towards the beginning. To improve our factory, for example, we need to fix the machines that produce the final product. Then, we fix the machines that produce components and then the ones that produce raw materials. We then fix the workers that work with those machines.
This method is known as kaizen because it focuses upon improving every aspect of the process step by step. After we're done with the factory, it's time to go back and fix the problem.
Before you can implement kaizen into your business, it is necessary to learn how to measure its effectiveness. There are many ways you can determine if kaizen has been implemented well. Another way to determine if kaizen is working well is to look at the quality of the products. Another way is to see how much productivity has increased since implementing kaizen.
Another way to know whether kaizen is working is to ask yourself why did you decide to implement kaizen. Is it because the law required it or because you want to save money. You really believed it would make you successful?
Let's say you answered yes or all of these questions. Congratulations! You're now ready to get started with kaizen.